Georgia Tech Faculty and Students Win Awards, Present Research at Design Automation Conference
Jul 26, 2022 — Atlanta, GA

Members of the Georgia Tech School of Electrical and Computer were well-represented at the 59th Design Automation Conference (DAC), a premier event devoted to the design and design automation of electronic chips and systems, was held in San Francisco on July 10-14.
The 59th Design Automation Conference (DAC), a premier event devoted to the design and design automation of electronic chips and systems, was held in San Francisco on July 10-14. The conference offers training, education, exhibits, and networking opportunities for designers, researchers, tool developers and vendors. It is sponsored by the Association for Computing Machinery (ACM) and the Institute of Electrical and Electronics Engineers (IEEE), and is supported by ACM's Special Interest Group on Design Automation (SIGDA) and IEEE's Council on Electronic Design Automation (CEDA).
In the span of five days, DAC provided over 300 technical presentations and sessions that were selected by a committee of electronic design and university research experts offering information on recent developments and trends, management practices and new products, methodologies, and technologies in the electronics industry.
“DAC brings together researchers across the computing stack — technology, circuits, design-automation and computer architecture — enabling a confluence of ideas and cross-stack research," said associate professor Tushar Krishna in the Georgia Tech School of Electrical and Computer Engineering. “It provides a multitude of opportunities for researchers, students, and industry experts to collaborate and influence tomorrow’s innovations, making it a highly exciting and effective conference.”
Faculty members and students in ECE were presented with multiple awards and participated in research talks and technical sessions. ECE’s DAC awards and contributions are listed below:
Awards:
- Professor Sung Kyu Lim and his students Bon Woong Ku (currently at Synopsys) and Kyungwook Chang (currently at Sungkyunkwan University) received the 2022 Donald O. Pederson Best Paper Award for their paper “Compact-2D: A Physical Design Methodology to Build Two-Tier Gate-Level 3D ICs” published in IEEE TCAD.”
- Ph.D. candidate Poulami Das (supervised by professor Moin Qureshi) won the “Best Research Award” during the Ph.D. Forum.
- Ph.D. candidate Rishov Sarkar (supervised by assistant professor Callie Hao) won the third place in the “University Demo Best Demonstration.”
- Ph.D. candidates Foroozan Karimzadeh (supervised by ECE chair Arijit Raychowdhury), Zishen Wan (supervised by Raychowdhury), and Anurag Kar (supervised by professor Hyesoon Kim in Tech’s School of Computer Science) were named 2022 DAC Young Fellows and presented on their respective research during the DAC Young Fellows Program workshop.
Engineering Talks, Tutorials, Workshops, Panels
- Hao gave an invited talk entitled, “3U-EdgeAI: Ultra-Low Memory Training, Ultra-Low Bitwidth Quantization, and Ultra-Low Latency Acceleration” during the Fifth International Workshop on Design Automation for Cyber-Physical Systems (DACPS).”
Hao, along with Hyoukun Kwon (a recent Ph.D. graduate supervised by Krishna and now at Meta), presented the tutorial “A Journey to SW/HW Co-design in Machine Learning: Fundamental, Advancement, and Application.” They presented twice on the same day due to tutorial’s popularity.
Hao was also the co-organizer of the Early Career Workshop for junior faculty and senior Ph.D. students interested in academia.
- Krishna presented an invited talk entitled, “Formalizing Design-space Exploration for Flexible AI Accelerators” during the Silicon Integration Initiative Low-Power Forum.”
- Lim presented at the engineering track Machine Learning and EDA: The Productivity Cycle and organized the research panel “Heterogeneous 3D or Monolithic 3D, Which Direction to Go?”
Technical Sessions
- Ananda Samajdar (recent Ph.D. graduate supervised by Krishna and now at IBM) presented his work “Self-Adaptive Reconfigurable Arrays (SARA): Learning Flexible GEMM Accelerator Configuration and Mapping-space using ML.”
- Ph.D. candidate Brian Crafton (supervised by Raychowdhury) presented his work “Improving Compute In-Memory ECC Reliability with Successive Correction”.
- Hao presented her work “H2H: Heterogeneous Model to Heterogeneous System Mapping with Computation and Communication Awareness”.
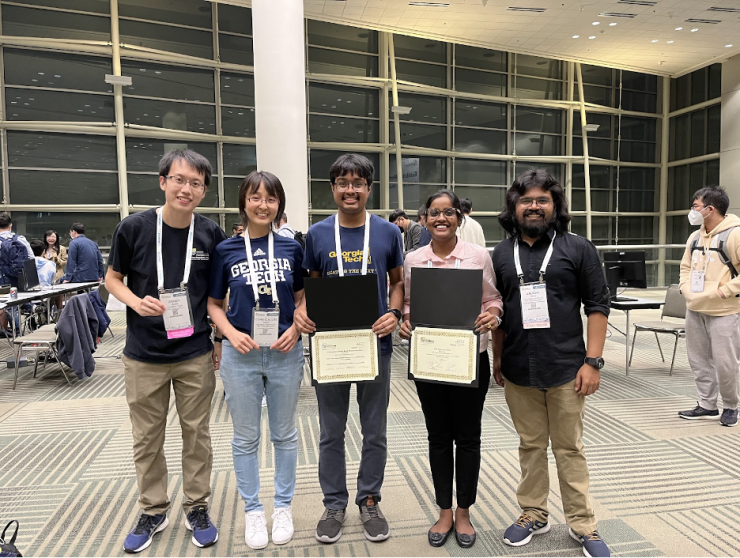
L-R: Zishen Wan (Ph.D. candidate), Callie Hao (assistant professor), Rishov Sarkar (Ph.D. candidate), Poulami Das (Ph.D. candidate), and Anurag Kar (Ph.D. candidate) all won awards at DAC.
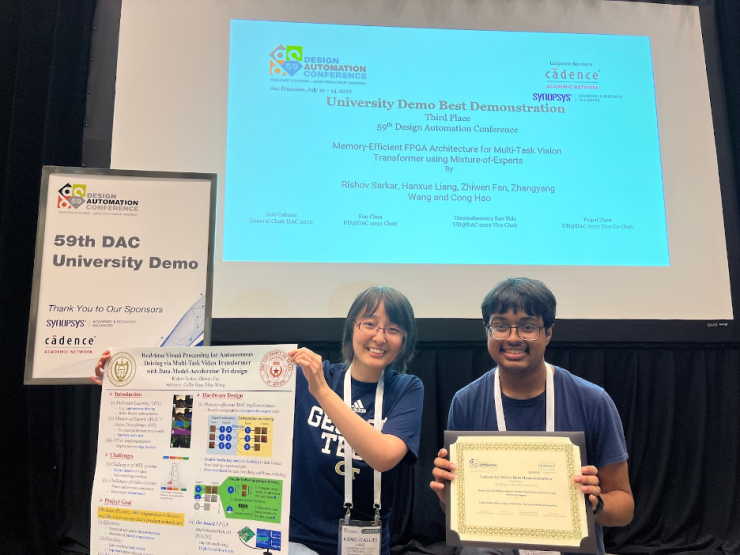
Ph.D. candidate Rishov Sarkar (right) won third place in “University Demo Best Demonstration.” He is supervised by ECE assistant professor Callie Hao (left).
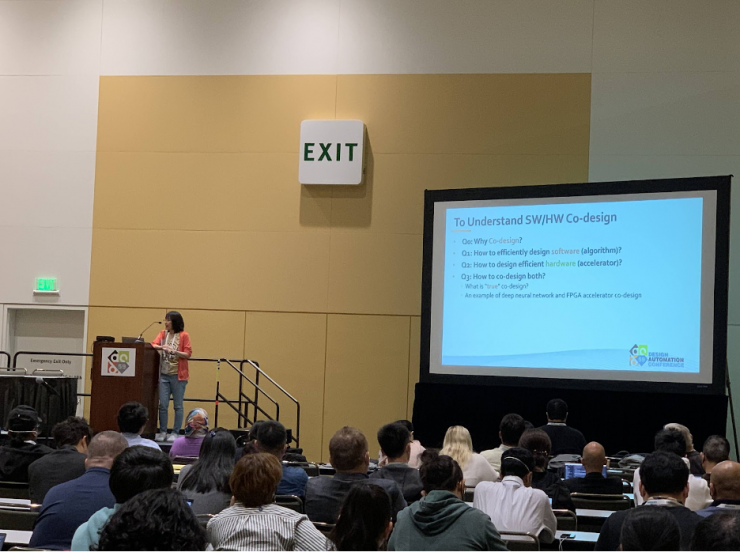
ECE assistant professor Callie Hao presenting the popular tutorial “A Journey to SW/HW Co-design in Machine Learning: Fundamental, Advancement, and Application.”
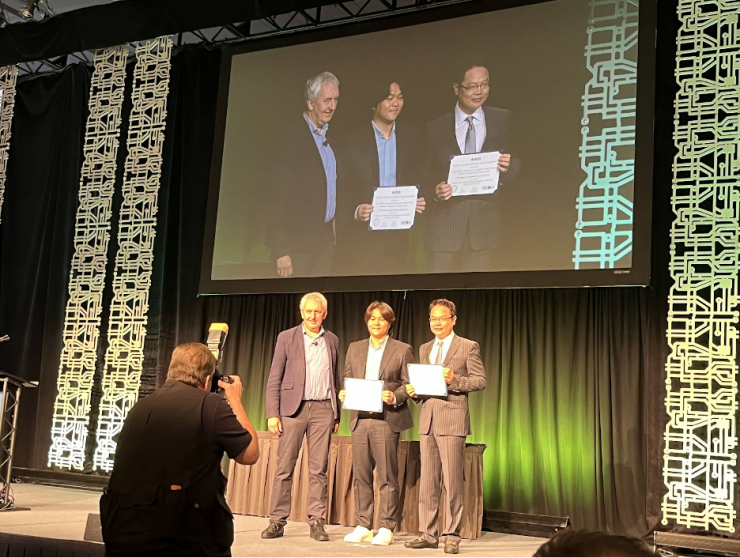
Professor Sung Kyu Lim (right) and his former student Bon Woong Ku (middle) receiving the 2022 Donald O. Pederson Best Paper Award for their paper “Compact-2D: A Physical Design Methodology to Build Two-Tier Gate-Level 3D ICs” published in IEEE TCAD.”
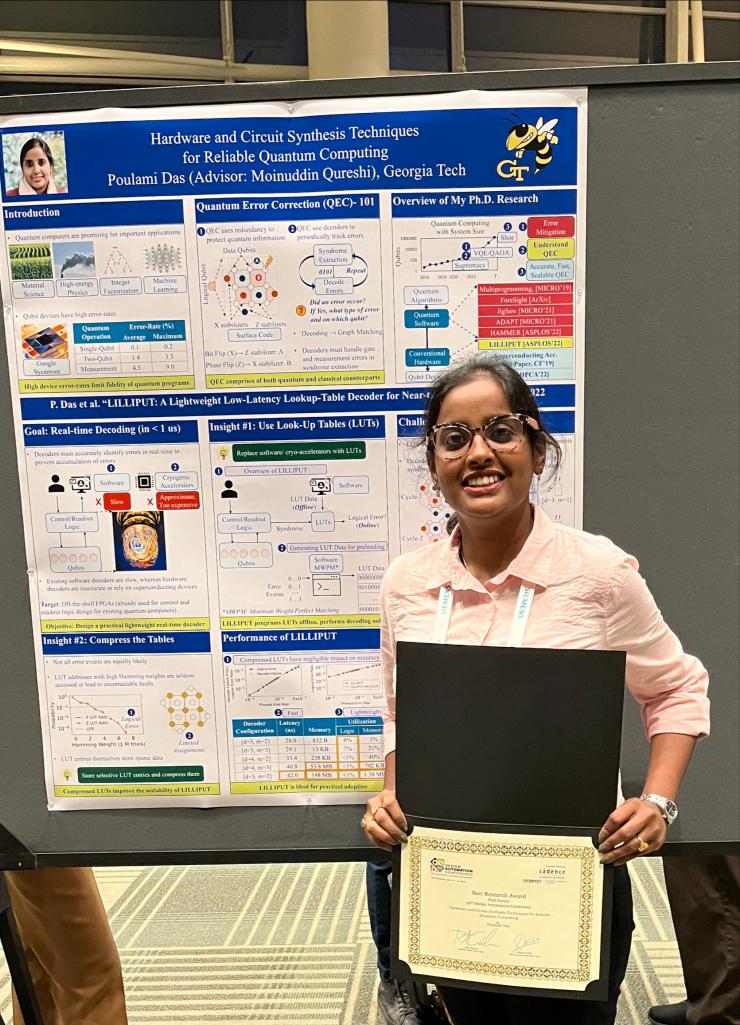
Ph.D. candidate Poulami Das won the “Best Research Award” during the Ph.D. Forum at DAC.
Dan Watson
dwatson@ece.gatech.edu
IEN Networking Lunch
Calling all researchers!
All Georgia Tech faculty and researchers are invited to join leaders from the Institute for Electronics and Nanotechnology (IEN) and their colleagues from across campus for an informal, no-host networking lunch. This is a great opportunity to learn more about IEN, its research areas, and potential partnership opportunities.
IEN Networking Lunch
Calling all researchers!
All Georgia Tech faculty and researchers are invited to join leaders from the Institute for Electronics and Nanotechnology (IEN) and their colleagues from across campus for informal, no-host networking lunches. These are a great opportunity to learn more about IEN, its research areas, and potential partnership opportunities.
IEN Networking Lunch
Calling all researchers!
All Georgia Tech faculty and researchers are invited to join leaders from the Institute for Electronics and Nanotechnology (IEN) and their colleagues from across campus for informal, no-host networking lunches. These are a great opportunity to learn more about IEN, its research areas, and potential partnership opportunities.
Large-area Flexible Organic Photodiodes Can Compete With Silicon Devices
Spontaneous Formation of Nanoscale Hollow Structures Could Boost Battery Storage
Baking and Boiling Botnets Could Drive Energy Market Swings and Damage
Nanoscale "worms" provide new route to nano-necklace structures
NNCI Webinar: Education and Computation
Virtual Immersive Worlds for Experiential Learning of Quantum and Semiconductor Physics
Featuring Professor Azad Naeemi | School of Electrical and Computer Engineering at Georgia Tech.
Short Course on Bioelectromagnetics: Principles and Applications
This course is led by Professor Christian Schuster from Hamburg University of Technology.
The field of bioelectromagnetics can be loosely defined as the science of electromagnetic field interaction with biological tissue. It is a subdiscipline of biomedical engineering and has many connections to medical and biological imaging, electrotherapy, electrophysiology, biophysics, bioelectronics, electromagnetic compatibility, and safety as well as electrochemistry.