Virtual Lecture Series at the Paper Museum
Aug 26, 2021 — Atlanta, GA
Dr. Nick Wilding
The Robert C. Williams Museum of Papermaking is hosting a virtual talk and discussion series entitled “The Book: Past, Present, and Future.” The series explores the forms and purposes of books as methods of communication. Scholars with expertise in each aspect – what books and their use have been, how society uses books now, and the possibilities of the future – will share with audiences the origins and use of these objects.
Talk 1: “The Book: The Past”
Tuesday, September 14, 2021, 8-9pm
Speaker: Dr. Nick Wilding, Georgia State University
Dr. Nick Wilding of Georgia State University will explore how books developed and were used over time. After Dr. Wilding's talk, program participants are invited to discuss how past use and production of books affected how we learn and document information.
https://www.eventbrite.com/e/virtual-lecture-the-book-the-past-tickets-168324100917
Talk 2: “The Book: The Present”
Tuesday, October 12, 2021, 8-9pm
Speaker: Dr. Jesse Erickson, University of Delaware
Dr. Jesse Erickson, Coordinator of Special Collections, Assistant Professor of English, and Associate Director of the Interdisciplinary Humanities Research Center at the University of Delaware, to understand how a familiar object- the book- has become an integral part of our lives and how libraries and special collections are navigating the changing world of publishing.
https://www.eventbrite.com/e/virtual-lecture-the-book-the-present-tickets-168336479943
Talk 3: “The Book: The Future”
Tuesday, November 9, 2021, 8-9pm
Speaker: Dr. Sarah Werner, independent scholar, founder of Early Printed Books (https://www.earlyprintedbooks.com/)
E-readers, digitization, and the internet are changing the way people access books and content. In this lecture, The Book: The Future, Dr. Sarah Werner, an independent historian, will share how technological advances are allowing historic books to be utilized in new ways. After the talk, participants are invited to discuss the ways in which we use books may be different in the future.
https://www.eventbrite.com/e/virtual-lecture-the-book-the-future-tickets-168341807879
The series is funded by a grant from the Georgia Humanities Council. All programs are free to attend from the comfort of your own living room!
Meet the scholars:
Sarah Werner
Sarah Werner is an independent scholar of book history, early modern culture, and digital media based in Washington DC. She is the author of the recently published Studying Early Printed Books 1450–1800: A Practical Guide and the newly launched EarlyPrintedBooks.com. In combination, the two works provide an introduction to how books were made in the hand-press period and how we can study them today, in person and online. She is also the author of articles on feminist printing history, digital First Folios, an overview of the connections between book history and digital studies, and numerous pieces on Shakespeare in performance, as well as the author of Shakespeare and Feminist Performance and co-editor of PBSA. More about her scholarship and her consultancy work can be found at https://sarahwerner.net.
Jesse R. Erickson, Ph.D., MLIS
Jesse R. Erickson is the Coordinator of Special Collections and Digital Humanities, Assistant Professor in the Department of English in the College of Arts and Sciences, and Associate Director of the Interdisciplinary Humanities Research Center at the University of Delaware. He previously worked as a bibliographic researcher and archival processor in the Manuscripts Division of the Charles E. Young Research Library and the Center for Oral History Research at the University of California, Los Angeles. He recently served as the Vice President for Programs for the American Printing History Association. Currently, he serves on the editorial boards of the University of Delaware Press and Publishing History, and he is the co-editor for the Papers of Bibliographical Society of America. His research specializations are in ethnobibliography, alternative printing, non-canonical textuality, African American print culture, and the transnational publishing history of the works of Ouida.
Nick Wilding
Nick Wilding is Professor of History at Georgia State University, where he teaches Early Modern history, the history of science, and the history of the book. He is the author of Galileo’s Idol: Gianfrancesco Sagredo and the Politics of Knowledge (Chicago University Press, 2014), Faussaire de Lune: Autopsie d’une Imposture, Galilée et ses contrefacteurs (Bibliothèque Nationale de France, 2015) and a dozen research articles. He has held fellowships at Stanford, Cambridge, Columbia, the American Academy in Rome, the New York Academy of Medicine, the Cullman Center at the New York Public Library and the Andrew W. Mellon Fellowship of Scholars in Critical Bibliography, Rare Book School. He currently serves on the Council of the Bibliographical Society of America and is a faculty member at Rare Book School. He received his B.A. in English from Oxford University, his M.A. in Renaissance Studies from the University of Warwick, and his PhD. in History from the European University Institute, Italy.
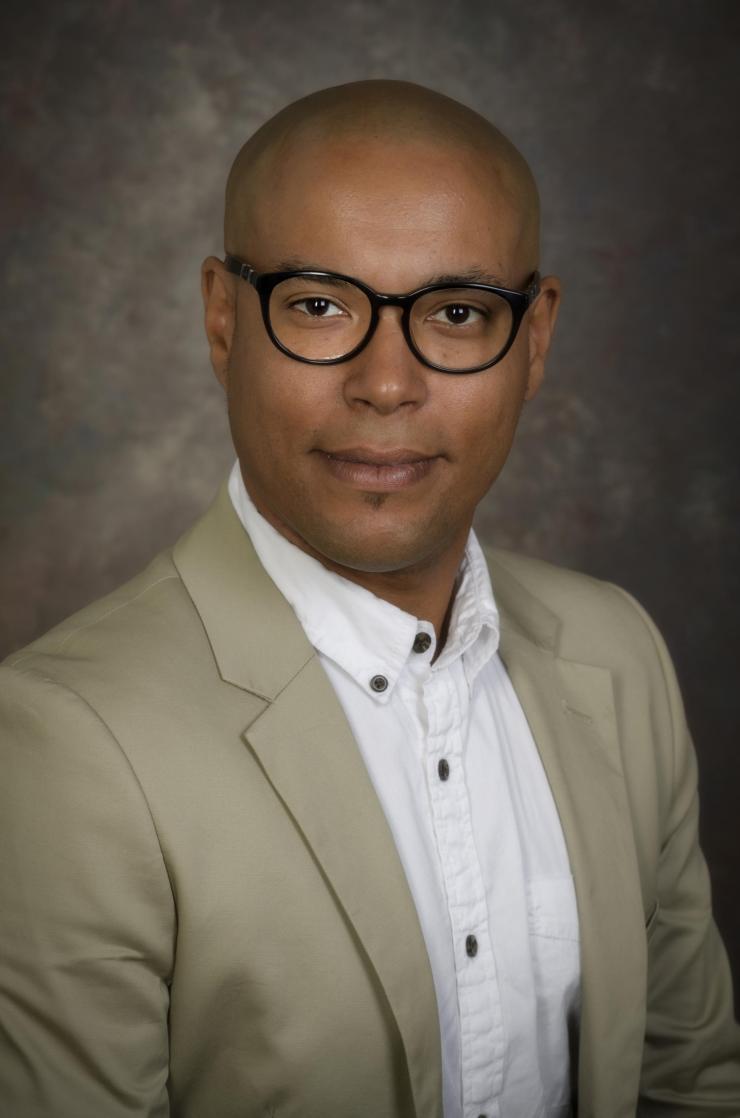
Dr. Jesse Erickson, speaker for "The Book: The Present" on October 12, 2021
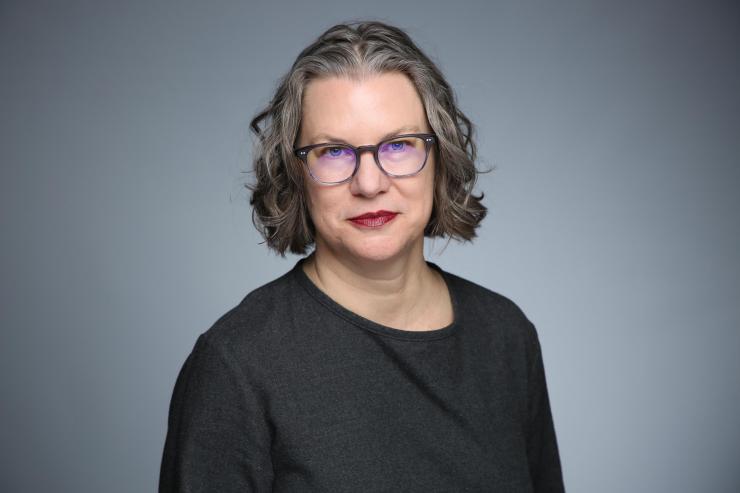
Dr. Sarah Werner will speak about the future of books in an increasingly digital world.
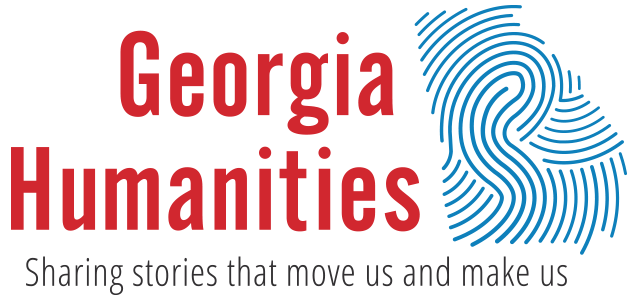
Georgia Humanities Council Logo
Virginia Howell
Museum Director
404-894-5726
virginia.howell@rbi.gatech.edu
Spring 2021 IEN Seed Grant Winners Announced
Jun 09, 2021 — Atlanta, GA
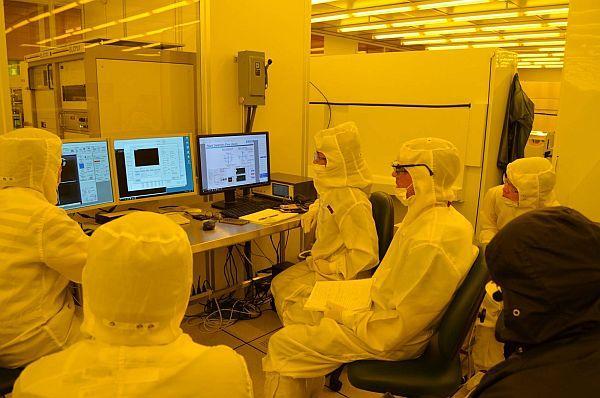
GT Researchers training on the Elionix E-Beam System in the IEN cleanroom, Marcus Nanotechnology Building, Atlanta Campus.
The Institute for Electronics and Nanotechnology at Georgia Tech has announced the winners for the 2021 Spring Facility Seed Grants. The primary purpose of this program is to give first- or second-year graduate students in diverse disciplines working on original and un-funded research in micro- and nano-scale projects the opportunity to access the most advanced academic cleanroom space in the Southeast. In addition to accessing the high-level fabrication, lithography, and characterization tools in the labs, the awardees will have the opportunity to gain proficiency in cleanroom and tool methodology and access the consultation services provided by research staff members of the IEN. Seed Grant awardees are also provided travel support to present their research at a scientific conference.
In addition to student research skill development, this bi-annual grant program gives faculty with novel research topics the ability to develop preliminary data to pursue follow-up funding sources. The Facility Seed Grant program is supported by the Southeastern Nanotechnology Infrastructure Corridor (SENIC), a member of the National Science Foundation’s National Nanotechnology Coordinated Infrastructure (NNCI).
Since the start of the grant program in 2014, sixty-eight projects from ten different schools in Georgia Tech’s Colleges of Engineering and Science, as well as the Georgia Tech Research Institute and 3 other universities, have been seeded.
The 3 winning projects in this round were awarded IEN cleanroom and lab access time to be used over the next year. In keeping with the interdisciplinary mission of IEN, the projects that will be enabled by the grants include research in biodevice development, new methodologies for tissue imaging, and design of water filtration membranes.
The Spring 2021 IEN Facility Seed Grant Award winners are:
Development of Lab-on-a-Chip Platform to Study the Extracellular Electron Transfer Processes
Student: Mourin Jarin | PI: Xing Xie
School of Civil and Environmental Engineering
Correlative 3D Metabolic and Structural In Situ Imaging of Human Tissues
Student: Thomas Hu (ECE) | PI: Ahmet Coskun
Wallace H. Coulter Department of Biomedical Engineering
Machine Learning-Assisted Design of Sustainable Nanofiltration Membranes for Wastewater Resource Recovery
Student: Dylan Lambeth | PI: Yongsheng Chen
School of Civil and Environmental Engineering.
- Christa M. Ernst
The Southeastern Nanotechnology Infrastructure Corridor (SENIC), a member of the National Nanotechnology Coordinated Infrastructure (NNCI), is funded by NSF Grant ECCS-2025462
Christa M. Ernst - Interdisciplinary Research Communications Program Manager
Topics: Materials | Nanotechnology | Robotics
Georgia Institute of Technology| christa.ernst@research.gatech.edu
5 Questions with the New IMat Advisory Team
Jun 09, 2021 — Atlanta, GA
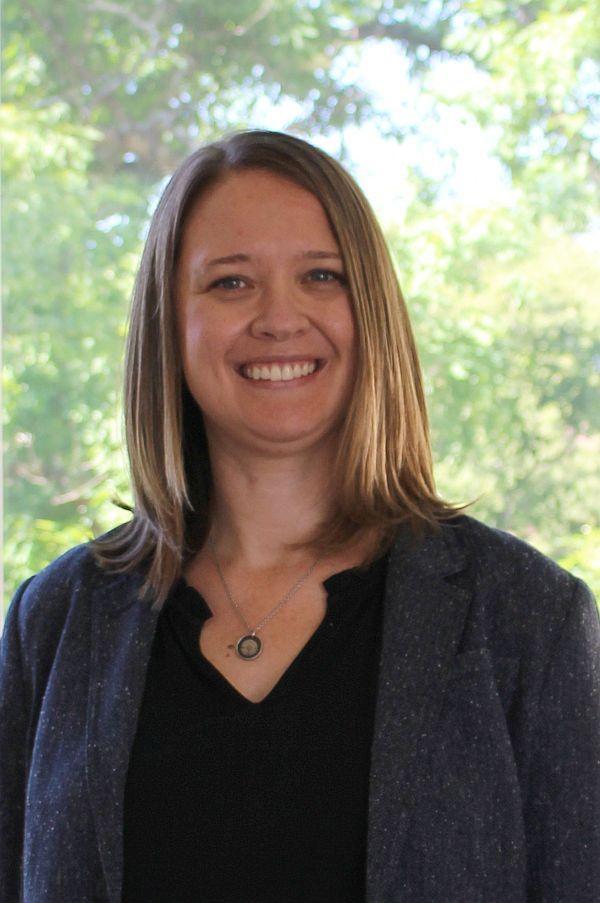
Blair K. Brettmann: Assistant Professor & Solvay Faculty Fellow, Co-Director; Georgia Tech Polymer Network, School of Chemical and Biomolecular Engineering & School of Materials Science and Engineering
1. What is your field of expertise and at what point in your life did you first become interested in this area?
Polymers. I worked with polymers in my PhD, but only used them as carrier materials and never dug deeper into the science or their properties. When I worked in industry for Saint-Gobain, I was in a polymer group and discovered how complex and interesting polymer science and especially polymer processing could be, so I decided to focus more on them moving forward.
2. What questions or challenges sparked your current materials research?
Polymers are long chain molecules, so they behave very differently than other material types. They have slow changes in properties since they need time to move, they behave differently when the chain is stretched out vs distributed throughout a globule and they have many chemical functional groups that can interact with other components in a mixture. If we can understand all these complex phenomena, we can more quickly design new and improved polymer-based products and even understand how to better recycle or remove them from the environment.
3. Why is your theme area important to the development of Georgia Tech’s Materials research strategy?
A major challenge for materials engineers today is working towards a more sustainable world, including for consumer products, many of which contain polymers either as their primary component or as a coating or binder. Georgia Tech has the base polymer community to become a leader in solving polymer sustainability challenges, both in designing new polymer systems and in better end of life for existing ones. Strategically drawing this group together will better allow our expertise and talents to make a difference in materials sustainability.
4. What are the broader global and social benefits of the research you and your team conduct?
Consumer plastics and polymer-containing materials are ubiquitous in the modern world and have led to many excellent outcomes in public health, preventing food spoilage, light weighting materials and more. However, they also are increasingly of concern for the environment through poor end of life degradation and challenges in recycling. Research to better understand polymers, fully integrating fundamental science and engineering design, is necessary to provide better plastics and processing for end-of-life.
5. What are your plans on engaging a wider GT faculty pool with IMat research?
I plan to partner with the Georgia Tech Polymer Network and host a series of discussions with applications specialists in consumer and industrial materials to understand the polymer science challenges in these areas and build bridges between applications and polymer faculty. I also plan to build on Georgia Tech’s core strengths related to consumer-focused polymers including polymer upcycling, machine learning for polymer design and polymer processing to link the experts to specific challenges across campus.
Christa Ernst | christa.ernst@research.gatech.edu
Krista Walton Named Interim Chair of the School of Chemical and Biomolecular Engineering
May 11, 2021 — Atlanta, GA
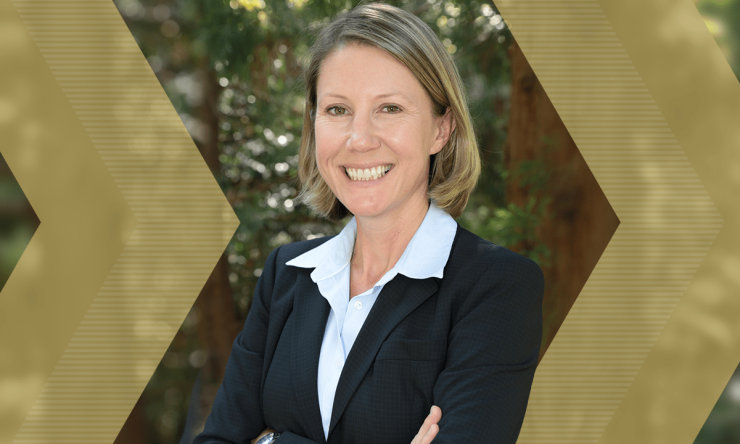
Krista Walton Named Interim Chair of the School of Chemical and Biomolecular Engineering
Effective July 1, 2021, Krista Walton, associate dean for Research and Innovation in the College of Engineering, Robert "Bud" Moeller Faculty Fellow, and professor, will serve as interim chair for the School of Chemical and Biomolecular Engineering.
Walton will begin her interim role in July after the current chair, David Sholl, transitions to a joint appointment with Georgia Tech and the Oak Ridge National Laboratory (ORNL). At ORNL, Sholl will be the director of the Laboratory's new Transformational Decarbonization Initiative.
“David has spent the last eight years working tirelessly for the School,” said Walton. “During his tenure, rankings improved, the School became more diversified, and additional funds were raised to drive student innovation. I have a strong, personal connection to ChBE where I’ve worked for the past 12 years and am honored to help us transition to a new chair.”
Walton currently serves as the associate dean for Research and Innovation in the College. She will continue in this role, while also serving as interim chair.
“Before becoming associate dean for the College, Krista began her career in the School of Chemical and Biomolecular Engineering, serving as a professor and faculty fellow,” said Raheem Beyah, dean and Southern Company chair of the College of Engineering. “She has excellent working relationships with the faculty and staff of the School, and I have every confidence she will continue the upward trajectory of both teaching and research to ensure the School thrives while we search for a new chair.”
Walton’s research focuses on the design, synthesis, and characterization of functional porous materials for use in adsorption applications, including carbon dioxide capture and air purification. Walton’s accomplishments have been recognized by many prestigious awards, including the Department of Energy’s Ernest Orlando Lawrence Award in honor of her contributions to the fields of atomic, molecular and chemical sciences (2021); the inaugural International Adsorption Society Award for Excellence in Publications by a Young Member of the Society (2013); and the Presidential Early Career Award for Scientists and Engineers (2008). Walton currently serves as an Associate Editor for the ACS Journal Industrial & Engineering Chemistry Research, and was the founding Director and Lead Principal Investigator of Georgia Tech’s Department of Energy – Energy Frontier Research Center, UNCAGE-ME.
Walton received her B.S.E. in chemical engineering from the University of Alabama-Huntsville in 2000 and obtained her Ph.D. in chemical engineering from Vanderbilt University in 2005. She also completed a postdoctoral fellowship at Northwestern University in 2006.
Search Committee Named
Dr. Samuel Graham, Eugene C. Gwaltney, Jr. Chair of the George W. Woodruff School of Mechanical Engineering, will chair the search committee tasked with finding a permanent chair. An External Advisors group of alumni and supporters is also being formed to help guide the search process. This will be an international search.
The Search Committee includes:
Blair Brettmann – Assistant Professor
Julie Champion – Associate Professor
Christian Cuba-Torres – Lecturer
Michael Filler – Associate Professor
M.G. Finn – School Chair, Chemistry and Biochemistry
Yoyin Ibikunle – Graduate Student
Kiyana Jacobs – Staff
Shelbe Johnson – Undergraduate Student
Paul Kohl – Regents’ Professor
Carson Meredith – Professor
Sally Ng – Associate Professor
Ami Waller-Ivanecky – Staff
Andrew Medford – Assistant Professor
Sankar Nair – Professor
Donna Peyton – Staff
Krista Walton – Professor
Corey Wilson – Associate Professor
In-depth Review of Nanomaterial Innovations in Water Purification Technology
May 10, 2021 — Atlanta, GA
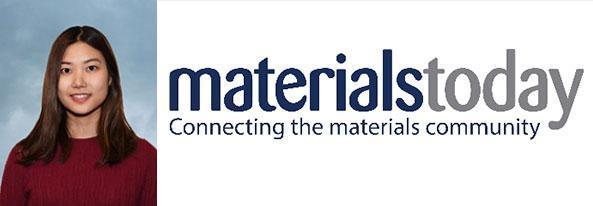
Jiwoo Yu, Ph.D., a graduate of the Paper Science and Engineering program within the Renewable Bioproducts Institute at Georgia Tech.
Jiwoo Yu, Ph.D., a graduate of the Paper Science and Engineering program within the Renewable Bioproducts Institute at the Georgia Institute of Technology recently published an article on “Water Treatment via Non-membrane Inorganic Nanoparticles/cellulose Composites” published in Materials Today, May 8, 2021.
The article offers an in-depth review of nanomaterials innovations in water purification technology. The paper highlights inorganic nanoparticles/cellulose hybrid nanocomposites which have attracted growing interest due to the unique properties of cellulose and high specific surface area of nanoparticles and their ability to target specific pollutants in water.
The integration with cellulose brings benefits to inorganic nanoparticle for water treatment, including preventing agglomeration, ensuring colloidal stability, and allowing for separation by magnetic nanoparticles after purification.
The full article, available on May 8, 2021, can be found online here at Materials Today.
This work was supported by the Renewable Bioproducts Institute (Grant number: GTF114000086) at the Georgia Institute of Technology.
The Renewable Bioproducts Institute at Georgia Tech offers top students an opportunity to conduct cutting-edge research to advance technologies and applications in the bioeconomy, advised by world-recognized experts and supported by four-year graduate research fellowships.
Walter Rich
Research News
Georgia Institute of Technology
RBI Student Internationally Recognized for Innovative Forest-based Industry Research
Apr 29, 2021 — Atlanta, GA
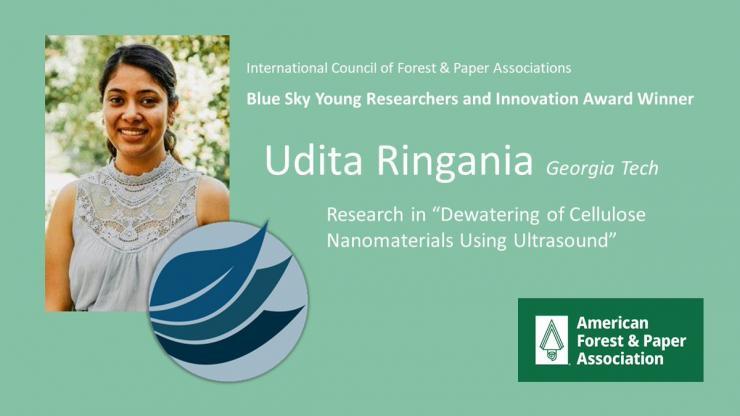
Udita Ringania, a Ph.D. candidate funded by the Renewable Bioproducts Institute’s (RBI) Paper Science & Engineering (PSE) Program at Georgia Tech
Udita Ringania, a Ph.D. candidate funded by the Renewable Bioproducts Institute’s (RBI) Paper Science & Engineering (PSE) Program at the Georgia Institute of Technology won the 2021 Blue Sky Young Researchers and Innovation Award.
The award is given by the American Forest & Paper Association (AF&PA) and the International Council of Forest and Paper Associations (ICFPA). Ringania was one of three scientists awarded at the 2021 ICFPA-hosted Global CEO Roundtable, a biennial gathering of forest product industry associations and leaders.
Launched in 2016, the international contest recognizes, celebrates and promotes noteworthy innovations being developed in the global forest sector by students, researchers and engineers age 30 years and younger.
Ringania was recognized for her research project, Dewatering of Cellulose Nanomaterials Using Ultrasound. She is a PSE fellow in the lab of Saad Bhamla, assistant professor in the School of Chemical and Biomolecular Engineering.
“Udita Ringania’s research is an impressive example of innovation in the forest products industry with great potential to help paper and packaging manufacturers advance sustainability,” said Heidi Brock, AF&PA president and CEO. “On behalf of AF&PA and our members, we congratulate Udita and look forward to seeing this exciting research progress.”
The theme for the 2020-2021 award program was “Boosting the Forest Bioeconomy: Nature-Based Solutions Toward a Lower Carbon Economy.”
In addition to Ringania, two other international finalists were recognized:
Jesús Rodríguez of Chile for research, Flexbio, A Biodegradable and Compostable Bioplastic. Radiata Pine Sawdust Derivative.
Francine Ceccon Claro of Brazil for research, Low Cost Wood-Derived Nanocellulose Wound Dressing.
AF&PA and TAPPI manage the U.S. Blue Sky Award application and selection process, nominating up to three candidates for the international competition. The U.S. judging panel was organized by the Alliance for Pulp & Paper Technology Innovation.
The international Blue Sky Awards program is sponsored by the ICFPA, a worldwide network of forest and paper associations that promotes cooperation in areas of common interest to its members and serves as the industry’s advocate at the international level.
The 2021 Blue Sky Award competition included 21 contestants from nine countries around the world. This year’s judging panel included representatives from the Food and Agriculture Organization of the United Nations, United Nations Forum on Forests Secretariat, International Union of Forest Research Organizations, Monash University and University of British Columbia.
The top three finalists presented their work at the ICFPA’s virtual Global CEO Roundtable discussion and were awarded cash prizes for their achievement. Mike Doss, president and chief executive officer for Graphic Packaging presented Ringania with her award.
“The Blue Sky Awards are proof of a vibrant, bright future for an essential and sustainable forest products industry,” said Doss. “The talent and innovation demonstrated by this year’s finalists is impressive.”
Learn more about the ICFPA Blue Sky Awards and 2021 award-winning research projects at: icfpa.org
Walter Rich
Research News
Georgia Institute of Technology
2021 Institute for Materials + BASF Graduate Student Fellows Announced
Apr 07, 2021 — Atlanta, GA
Georgia Tech’s Institute for Materials (IMat), with generous support from BASF, is pleased to announce the 2021 IMat Graduate Student Fellows (IGSF). The 4 awardees will receive a $3K direct funding grant to supplement their existing monthly stipends during the award year. The winners were selected based on their projects’ view to materials sustainability regarding raw materials, carbon or energy efficiency, or waste and recyclability.
Krista Bullard
Utilizing Cyclodextrin to Compatibilize the Polymer and CNC Interface for Lightweight Material
Advisors: Will Gutekuhst; Professor, School of Chemistry and Mohan Srinivasarao; Professor, School of Materials Science & Engineering
As a renewable resource, cyclodextrin-modified CNCs have the potential to produce a new class of lightweight, high-strength composites for a wide-range of applications, including materials in the automotive and aerospace fields. The research this award will support involves using my recently developed surface modification technique to covalently anchor cyclodextrin rings onto cellulose nanocrystal (CNC) particles and study the physical threading of polymers through the cyclodextrin cavity
Receiving the IMat Graduate Fellowship is incredibly exciting and a great motivator as I am working on a challenging section of my project while working with lab restrictions. I am grateful to BASF for these funds, and I am excited to share my progress later in the year.
- Krista Bullard
Krista received her B.S. in chemistry at the University of Pittsburgh. While at Pitt, she conducted computational research on silyl ketene polymerization and CO2 absorption in ionic liquids with Dr. Daniel Lambrecht. During the summer of 2016, Krista received the Mickey Leland Energy Fellowship through the Department of Energy at the National Energy Technology Lab in Pittsburgh, where she did computational research of the electrochemistry of CO2 with gold nanoparticles. In the summer of 2017, Krista worked in polymer R&D at Sherwin-Williams. She is currently a PhD candidate in the School of Chemistry and Biochemistry and a recipient of the Renewable Bioproducts Institute fellowship.
Karoline Hebisch
Mechanocatalytic Ammonia Synthesis over Transition Metal Nitrides in Transient Microenvironments
Advisor: Carsten Sievers; Associate Professor, School of Chemical & Biomolecular Engineering
Hebisch and team aim to provide an alternative to the current way to produce fertilizers based on ammonia, which is currently highly industrialized and only viable at large scale, to enable increasing agricultural yields in developing regions. Their mechanocatalytic approach offers a promising alternative to industry use standards, as it can operate with renewable energy sources and features a simple, modular design.
The award of this fellowship shows that industry leaders also see a potential for our research to play a role in a more sustainable future and the funding provided will help to continue our pioneering work on this important topic.
- Karoline Hebisch
Karoline L. Hebisch is a second-year Ph.D. student in the School of Chemical & Biomolecular Engineering. She is advised by Dr. Carsten Sievers in the field of heterogeneous catalysis.
Karoline received her B.S. and M.S. in Chemistry from the Technical University of Darmstadt in 2016 and 2019. During her master’s she spent a semester abroad to study Plastics Engineering at the University of Massachusetts, Lowell. In her master’s thesis with Dr. Sievers, she studied mechanochemical ammonia synthesis as a sustainable, distributed approach for fertilizer production.
Emily Klein
Developing and Understanding Liquid Metal Interfaces for Solid-State Batteries
Advisor: Matthew McDowell; Associate Professor, School of Mechanical Engineering and the School of Materials Science & Engineering
To make renewable energy possible for our society, progress needs to be made to improve energy storage devices. Fundamentally understanding the effects of liquid metals at solid- solid electrochemical interfaces will be an important step toward making solid-state batteries a competitive energy storage option. Our team aims to produce research results that help drive the development of batteries with higher energy density and specific energy that can be produced at scale for wide adoption.
Due to recent environmental disasters such as fires and hurricanes, climate change is again at the forefront of public discussion. New battery technologies will be critical for enabling longer- range electric vehicles and for the engineering of largescale energy storage technologies to mitigate greenhouse gas emissions for our society.
- Emily Klein
Emily Klein is a first-year graduate student in the School of Materials Science and Engineering, working in Prof. Matthew McDowell’s group and leading a research project focused on interfacial engineering of solid-state batteries. She has extensive prior research experience on investigating battery safety during her co-op experience at the Naval Research Lab, and is excited to be working to enable the creation of next generation solid-state batteries.
Sai Saravanan Ambi Venkataramanan
High-Throughput Screening of Cathode-Electrolyte Systems for Stable Lithium-Air Battery (LAB) Design using Machine-Learning (ML) and Density Functional Theory (DFT) Simulations
Advisor: Seung Soon Jang; Professor, School of Materials Science and Engineering
Machine Learning advances are aiding the development of reliable computational screening models for new energy storage devices. Unlike (de)intercalation in Lithium-ion batteries, Lithium-Air batteries requires an understanding of various competitive reactions taking place at both the cathode surface and solvated electrolyte. Training a machine learning model using data from molecular simulations can help us to predict battery performance for a wide array of substrates.
US Department of Energy aims to reduce price of batteries to about $80-100/kwh. There is an uprising need to develop cheap, energy dense, and compact devices. I am fortunate to study on fundamental mechanism of Lithium-air batteries, at this right hour. I am grateful to my advisor, Institute for Materials, and BASF for believing in and funding this project.
- Sai Saravanan Ambi Venkataramanan
Sai Saravanan Ambi Venkataramanan received his B.S in Chemical Engineering, with an emphasis on ASPEN and molecular simulations in studying the extraction efficiency of ionic liquids. He received the Indian Science Academies Summer Research Fellowship in 2018 and attended the CCP5-CECAM Summer Program in ‘Molecular Simulations of Condensed Phases’ at Lancaster University, UK. Sai is currently pursuing his M.S. in Materials Science and Engineering at Georgia Tech working under Prof. Seung Soon Jang in developing principal cathode and electrolyte specific features to predict Lithium-Air Battery performance.
The awardees will present their research to BASF representatives at BASF’s campus recruiting visit during October 2021. Fellows’ presentations will detail the aspects explored, new capabilities developed, and how their research impacts them personally and professionally, including benefits to their group, academic unit, Georgia Tech Community, and the larger society.
Founded in 2012 as one of Georgia Tech’s 11 interdisciplinary research institutes, the Institute for Materials at Georgia Tech seeks to enable and support Georgia Tech’s internationally recognized materials research and innovation ecosystem; establishing and supporting large- scale industry and government partnerships, developing opportunities for Georgia Tech researchers to catalyze new ideas, and establishing Georgia Tech as an internationally recognized hub for core materials research facilities, infrastructure and knowledge. Learn more at: https://research.gatech.edu/materials
The Georgia Institute of Technology, or Georgia Tech, is a top 10 public research university developing leaders who advance technology and improve the human condition.The Institute offers business, computing, design, engineering, liberal arts, and sciences degrees. Its nearly 40,000 students, representing 50 states and 149 countries, study at the main campus in Atlanta, at campuses in France and China, and through distance and online learning. As a leading technological university, Georgia Tech is an engine of economic development for Georgia, the Southeast, and the nation, conducting more than $1 billion dollars in research annually for government, industry, and society. For more on Georgia Tech research visit: https://research.gatech.edu/
BASF Corporation, headquartered in Florham Park, New Jersey, is the North American affiliate of BASF SE, Ludwigshafen, Germany. BASF has approximately 17,000 employees in North America and had sales of $18.7 billion in 2020. For more information about BASF’s North American operations, visit basf.com.
BASF, we create chemistry for a sustainable future. We combine economic success with environmental protection and social responsibility. More than 110,000 employees in the Group contribute to the success of our customers in nearly all sectors and almost every country in the world. Our portfolio is organized into six segments: Chemicals, Materials, Industrial Solutions, Surface Technologies, Nutrition & Care and Agricultural Solutions.BASF generated sales of €59 billion in 2020. BASF shares are traded on the stock exchange in Frankfurt (BAS) and as American Depositary Receipts in the U.S. Further information at basf.com.
- Christa M. Ernst - Interdisciplinary Research Communications Program Manager
Materials | Nanotechnology | Robotics
Georgia Institute of Technology| christa.ernst@research.gatech.edu
Georgia Tech Researchers Awarded Total of $4.35 Million in 2020 for Direct Air Capture Projects
Mar 09, 2021 — Atlanta, GA

Global Theromostat’s direct air capture installation in Huntsville, Alabama.
Researchers in Georgia Tech’s School of Chemical and Biomolecular Engineering (ChBE) are principal investigators on six new projects that have been awarded a total of $4.35 million for studies related to direct air capture science and technology. Direct Air Capture (DAC) is a technology that removes carbon dioxide (CO2) directly from ambient air for use as a feedstock for chemical processes or transformed into a durable substance so that it can be sequestered. Some of the proposed chemical transformations that are possible with this technology include liquid fuels that could serve as “drop-in” replacements for the petroleum-based fuels we use for transportation.
With these recent awards, Georgia Tech researchers, with the support of Georgia Tech’s Strategic Energy Institute (SEI), have launched the Direct Air Capture Center (DirACC) under the guidance of Christopher Jones, Professor and William R. McLain Chair, and Matthew Realff, Professor and David Wang Sr. Fellow. DirACC will create a forum for collaborative research on NETs and DAC, bringing together researchers from across the Institute working in energy, sustainability, policy, and related fields.
For more than a decade, Georgia Tech researchers have worked to develop materials and processes that extract carbon dioxide directly from the atmosphere and transform it into something more durable or useful. In 2008, Jones began collaborating with the founders of a startup company, Global Thermostat, to develop materials and processes for DAC. His group first disclosed the use of hybrid silica/organic amine materials for CO2 capture from ambient air in 2009 at the American Institute of Chemical Engineers Annual Meeting. Global Thermostat’s core technology marries the CO2-sorbing materials developed by Jones’ group with a low energy process for ensuring good air contact with those materials. In 2015, Global Thermostat built their initial R&D facility in Georgia Tech’s Advanced Technology Development Center (ATDC), the nation’s oldest technology incubator. Global Thermostat operated its ATDC facility through the end of 2020, while building technology demonstration projects in Huntsville, Alabama, in 2019 and opening a new R&D facility in Denver, Colorado, in 2020.
In 2010, David Sholl, John F. Brock III School Chair, collaborated with Jones on what is believed to be the first federally funded DAC research project sponsored by the Department of Energy’s National Energy Technology Laboratory. The Camille and Henry Dreyfus Foundation played an early role in sponsoring DAC research at Georgia Tech as well. The foundation has recently produced a short film, featuring Jones, on the concept of DAC in its Chemistry Shorts film series, which is aimed at attracting young people to careers in STEM (chemistryshorts.org).
In 2017-18, Jones co-led a study on DAC technology for inclusion in the U.S. National Academies consensus study on Negative Emissions Technologies and Reliable Sequestration: A Research Agenda. This study adapted a technoeconomic analysis developed by Realff and former Georgia Tech Professor Yoshiaki Kawajiri (Nagoya University). The report explored all the terrestrial ways that CO2 could be removed from the atmosphere, including DAC with geologic sequestration, bioenergy with carbon capture and sequestration (BECCS), carbon mineralization, and coastal, forest, and soil management practices. (nap.edu/read/25259/chapter/1).
In parallel, researchers at Tech have engaged in related technology developments in carbon capture, with large, established technology firms. Examples include projects with ExxonMobil Research and Engineering Company led by Associate Professor Ryan Lively, along with M.G. Finn, professor and chair of the School of Chemistry and Biochemistry and the James A. Carlos Family for Pediatric Technology; William Koros, professor and Roberto C. Goizueta Chair for Excellence in Chemical Engineering; and Realff, focusing on a range of CO2 capture problems. ExxonMobil has supported R&D efforts in CO2 capture at Georgia Tech dating back to 2005. To date, the GT-ExxonMobil relationship has resulted in the graduation of 10 Ph.D. students, the support of five postdoctoral researchers, and has resulted in more than 45 papers and 25 US patents.
Beyond the fundamental science and engineering of DAC, other research efforts at Georgia Tech are modeling the implications of large-scale deployment of negative emissions technologies. Alice Favero, an environmental economist in the School of Public Policy, develops economic models to study how NETs can be balanced with the optimal use of land and other climate mitigation policies. Recently, she has collaborated with Lively and Realff on assessing the global potential for DAC. In this work, the concept of using sustainable Bio-Energy for Carbon Capture and Sequestration (BECCS) processes coupled with DAC technology allows for significantly greater atmospheric CO2 removal and avoids the complexity of connecting the biomass energy facility to the grid. In particular, Favero demonstrated that this technology can work in combination with ecological afforestation efforts that maintain or enhance the natural ecosystem services and avoid converting forested lands into plantations.
Georgia Tech is also conducting research on DAC methods that leverage the photosynthesis of plants other than trees to capture CO2 from the atmosphere to produce chemicals and fuels. Valerie Thomas, the Anderson-Interface Professor of Natural Systems in the H. Milton Stewart School of Industrial and Systems Engineering, has worked with biofuels companies Algenol and LanzaTech to perform life cycle assessments to determine the potential for their technologies to contribute to carbon sequestration. Using life cycle assessment to study biofuel production also reveals the possibility of unexpected impacts and suggests ways that negative consequences can be averted or mitigated.
Climate models now show that reduction of current and future emissions alone will not limit the global average temperature rise to 1.5-2 °C, the level suggested that may allow society to stave off the worst impacts of global climate change. These models suggest that negative emissions technologies, such as direct air capture, will need to be developed and deployed at a large scale to stabilize the climate. Georgia Tech researchers have done pioneering work in this area and are poised to continue advancing the state of the art.
Research News
Georgia Institute of Technology
177 North Avenue
Atlanta, Georgia 30332-0181 USA
Media Relations Contacts: John Toon (404-894-6986) (jtoon@gatech.edu) or Anne Wainscott-Sargent (404-435-5784) (asargent7@gatech.edu).
Writer: Brent Verrill
Brent Verrill
Research Communications
Professor Walton Wins DoE’s Ernest Orlando Lawrence Award
Jan 13, 2021 — Atlanta, GA
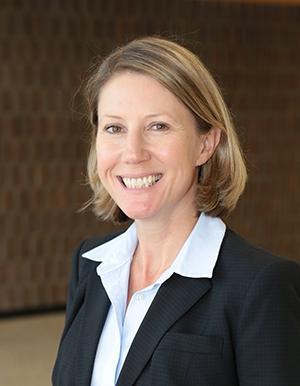
Professor Krista Walton of Georgia Tech’s School of Chemical and Biomolecular Engineering
Professor Krista Walton of Georgia Tech’s School of Chemical and Biomolecular Engineering is one of eight U.S. scientists and engineers to receive the Ernest Orlando Lawrence Award this year for contributions in research and development supporting the U.S. Department of Energy’s missions in science, energy, and national security.
Since 1959, the Lawrence Award has recognized mid-career scientists and engineers in the United States who have advanced new research and scientific discovery in atomic, molecular, and chemical sciences; biological and environmental sciences; computer, information, and knowledge sciences; condensed matter and materials sciences; energy science and innovation; fusion and plasma sciences; high energy physics; national security and nonproliferation; and nuclear physics.
“These researchers have made significant advances and contributions across a broad range of disciplines critical to Energy Department missions,” says U.S. Secretary of Energy Dan Brouillette. “We congratulate them on their many accomplishments and look forward to their achievements in the coming years.”
Walton (in the category of Atomic, Molecular, and Chemical Sciences) was honored for her “pioneering and interdisciplinary research of porous material stability under a variety of challenging conditions and advancing separation science. Working at the intersection of chemistry, computation, and chemical engineering, Walton has identified physical and chemical factors driving water stability of sorbents, especially metal-organic frameworks (MOFs), and the impact of defects and complex mixtures on the chemical stability of MOFs."
Walton is the Associate Dean for Research & Innovation in Georgia Tech’s College of Engineering and the Robert “Bud” Moeller Faculty Fellow.
Walter Rich
Bioindustrial Manufacturing Innovation Institute That Includes Georgia Tech Wins $87 Million Award
Dec 01, 2020 — Atlanta, GA
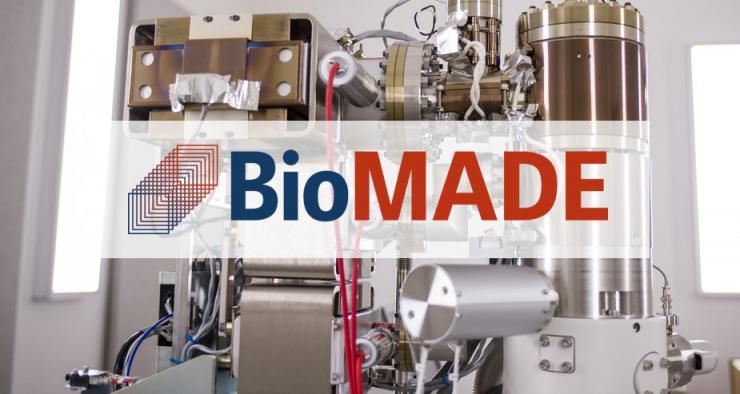
Biomade Logo. BioIndustrial Manufacturing and Design Ecosystem (BioMADE), a nonprofit that recently won a seven-year, $87 million award from the U.S. Department of Defense (DoD).
This story by Brad Dixon was first published to chbe.gatech.edu.
Georgia Institute of Technology is a governing member of the BioIndustrial Manufacturing and Design Ecosystem (BioMADE), a nonprofit that recently won a seven-year, $87 million award from the U.S. Department of Defense (DoD).
Created by the Engineering Biology Research Consortium, BioMADE will collaborate with public and private entities to advance sustainable and reliable bioindustrial manufacturing technologies. Headquartered at the University of Minnesota in St. Paul, BioMADE includes some of the largest bioindustrial manufacturing employers in the U.S. working in conjunction with some of the top educators in the world.
In support of this collaboration, the $87 million in DoD funding will be combined with more than $187 million in non-federal cost-share from 31 companies, 57 colleges and universities, six nonprofits, and two venture capital groups across 31 states.
Pamela Peralta-Yahya, faculty member of the Georgia Tech Renewable Bioproducts Institute, and associate professor in Georgia Tech’s School of Chemistry and Biochemistry, and School of Chemical and Biomolecular Engineering, is Tech’s representative to BioMADE’s Leadership Council, which will set the organization’s funding priorities.
Peralta-Yahya says, “An incredible cross section of Georgia Tech faculty contributed to the BioMADE proposal; over 30 faculty members, spanning five Schools across the College of Science, College of Engineering, and the Ivan Allen College of Liberal Arts.”
She notes: “Georgia Tech’s involvement in BioMADE is poised to catalyze interdisciplinary collaborations across the university, from data science and downstream processing to supply chain logistics and the policy, legal, and biosafety implications of bioindustrial applications. The projects funded by BioMADE will give undergraduates and graduate students a springboard to the emerging biomanufacturing and related areas.”
Mark Styczynski, an associate professor in Georgia Tech’s School of Chemical and Biomolecular who is Tech’s representative to the BioMADE Technical Committee, says: “Georgia Tech will be a member of BioMADE at the governing level, the highest level of engagement for academic institutions. We are excited about the resulting opportunities for Georgia Tech to bring to bear its manufacturing, chemical, and biochemical expertise on new applications and focus areas in the biomanufacturing space.”
He adds: “Our involvement in this area is a great complement to other biomanufacturing efforts at Georgia Tech and will contribute to a rapidly growing bioeconomy in Georgia.”
Through a close relationship with DoD and the Military Services, BioMADE will work to establish long-term and dependable bioindustrial manufacturing capabilities for a wide array of products. Anticipated bioindustrial manufacturing applications include the following products: chemicals, solvents, detergents, reagents, plastics, electronic films, fabrics, polymers, agricultural products (e.g. feedstock), crop protection solutions, food additives, fragrances, and flavors.
BioMADE’s efforts will examine and advance industry-wide standards, tools, and measurements; mature foundational technologies; foster a resilient bioindustrial manufacturing ecosystem; advance education and workforce development; and support the establishment and growth of supply chain intermediaries that are essential for a robust U.S. bioeconomy. Other important focus areas include challenges related to biosafety and security and ethical, legal, and societal considerations.
Stefan France, an associate professor in Georgia Tech’s School of Chemistry and Biochemistry is Tech’s representative to BioMADE’s Education and Workforce Committee, which will help craft and implement the organization’s strategic plan.
France explains that this committee “will concentrate its efforts in three major areas: curriculum and training for the bioindustrial workforce, promoting awareness of career opportunities, and coordination across the STEM community, the biomanufacturing ecosystem, and the training pipeline—everything from K-12 to community and technical colleges to four-year colleges, graduate programs, and post-graduate training.”
Brad Dixon, braddixon@gatech.edu